Systel offers customers with a wide range of aftermarket solutions and services. We Support you at every stage – from routine services, testing, spare part requirements, service level agreements to short/long-term rental options. With our ongoing maintenance and service packages, you can avoid costly breakdowns and keep your compressed air and other systems running at peak performance.
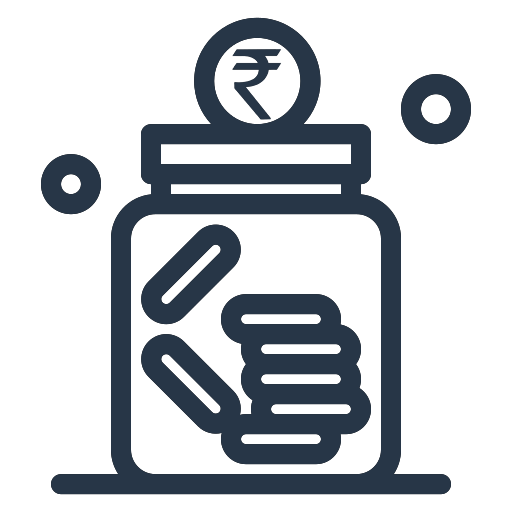
Significant Cost Savings
Systel provides targeted expertise and solutions that focus
on improving system performance and reduce energy consumption.
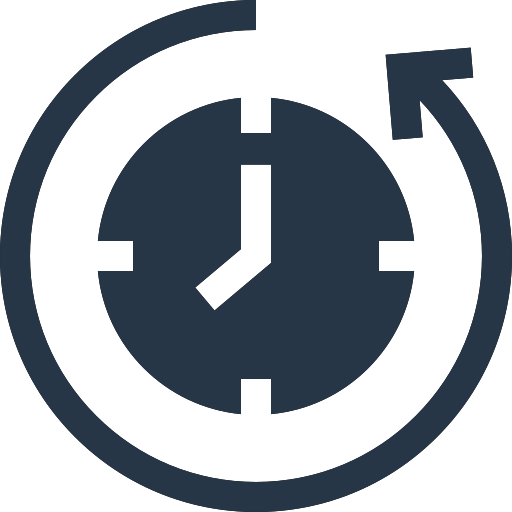
Reduced Downtime
Systel’s dedicated service engineers are always
available to ensure that your systems are performing
and functioning optimally.
Services we provide
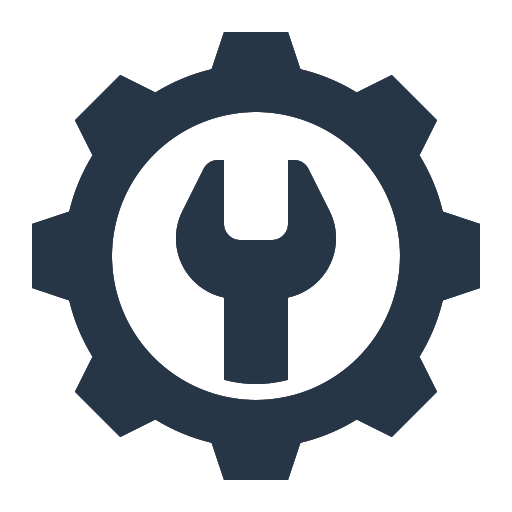
FIELD SERVICE & REPAIR
Maintaining your compressed air system at peak operating conditions ensures maximum performance, lower running costs, longer life with a substantially improved return on your investment. We operate a range of service schemes designed to meet our customers’ needs, from a periodic annual service to comprehensive schemes. Peace of mind guaranteed.
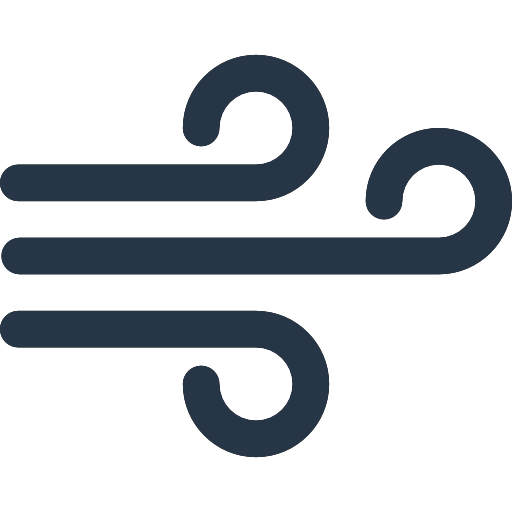
AIR PURITY TESTING
Many industries require a clean air supply in their production lines or manufacturing sites and for some sectors, quality of the air supplied to breathing apparatus is crucial. Systel ensures that you will benefit from our engineering knowledge, developed from decades of air quality testing experience. Systel provide customers with fully certified air quality test reviews to ISO 8573 Standards, ensuring that production facilities are fully compliant with industry standards avoiding any unnecessary and costly production downtime.
BENEFITS OF AIR PURITY TESTING :
Air purity testing can be applied to any industry or appliance utilising compressed air Testing with the latest equipment ensures timely data collection, analysis and practical recommendations including preventative action and breakdown avoidance. All testing is carried out in accordance with industry standards to ensure the highest safety levels are maintained at all times
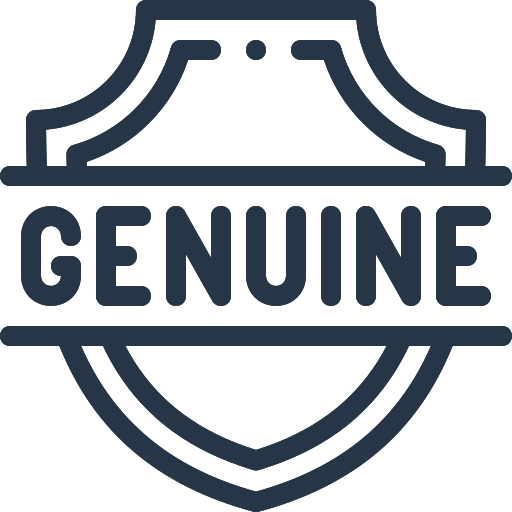
GENUINE OEM SPARE PARTS
Systel’s focus is to provide you instant access to a wide range of OEM spare parts and associated consumables from leading world class brands, to keep your business-critical compressed air operating to its highest specification.
We hold large stocks of genuine, recommended OEM spare parts to guarantee the longevity of your equipment to minimise your production downtime. Our factory trained technicians and technical support teams are on hand to give you the best advice when choosing appropriate parts or service kits.
BENEFITS OF FITTING GENUINE OEM SPARE PARTS :
• Manufacturer spare parts, when properly fitted will help maintain the reliability and long- running operation of your machinery.
• Our highly experienced team of industry trained engineers are ready to assist you with the best specification and fitting guidelines for all your spare parts
• Large stocks of genuine spare parts are readily available to eliminate risk of operational disruption
• The installation of genuine OEM spare parts will reduce unexpected maintenance costs and production downtime
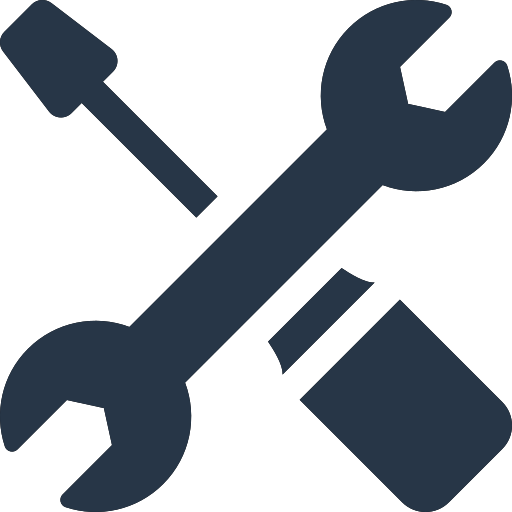
INSTALLATION & START UP
Our team of highly trained Sales Engineers are available to give on-site advice and technical support from initial specification, ordering and installation – right through to servicing and maintenance.
Installing and testing on site to ensure that it is working to full capacity, allowing you to run your business without the added hassle. We can save customers time and money and take the Pressure off you and your workforce.
During the installation process, Systel engineers will provide a full on-site assessment, initial Operator Training and We Can also work with your staff to ensure that our equipment is configured to how you need it in your production process.Upon completion of installation and commissioning, we will provide you with a comprehensive installation report containing a full breakdown of procedures undertaken and advice given. After installation, we also provide our customers with an ongoing technical helpline, backed up with full maintenance spares availability and servicing.